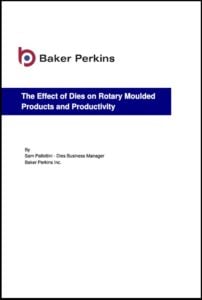
In a typical rotary moulder line, the die has more impact on the properties of the finished product and, arguably, on the efficiency of the line itself, than any other single piece of equipment. The direct effect that the die has on the appearance of the finished product is obvious, but there are more subtle effects too:
- inaccurate weight control leads to waste
- giveaway and packaging problems
- poor release results in excessive extraction pressure causing wedging and tailing
- incorrect choice of coating materials and finishes means rapid wear and frequent stops for cleaning because of plugging
All these problems can be avoided by good design and manufacture, but there is a lot more to achieving this than meets the eye. This paper examines the various options open to biscuit manufacturers when specifying a new die and considers the impact of each on performance and quality.
The full paper can be viewed here.