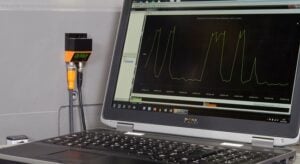
Until now, inspecting a gearbox on an extruder to determine whether repair or replacement was needed was time consuming and difficult.
The temptation has been to let a gearbox run and rely on recognizing changes in sound – rattling or squeaking – or obvious vibration before taking any action.
Even then, it’s quite likely that you could fix one problem, such as the bearings, only to find that the real issue is elsewhere. So you have to shut the machine down again, losing yet more production.
The answer is electronic gearbox condition monitoring: one of the most beneficial and cost-effective new features we have introduced on our twin-screw extruders for both the food and powder coating industries.
This simple low-cost system continuously monitors the frequency and amplitude of vibrations within the gearbox, allowing the ongoing condition of vital components to be measured. In effect it is doing what an experienced engineer would do – listening and feeling the gearbox for any signs of distress. The difference is that it does so continuously and can detect problems far earlier than a human.
Green, amber or red signals indicate that the gearbox is operating within limits; requires inspection or maintenance; or needs urgent attention. The easy-to-understand self-monitoring system is pre-calibrated for Baker Perkins extruder gearboxes, with transition points benchmarked and highlighted immediately on the ‘traffic light’ system.
Whenever there is a problem on the gearbox, it is flagged up well in advance so corrective action can be taken – before the business suffers. The system can detect problems caused by normal wear or by impending failures that might lead to a sudden stoppage.
Gearbox condition monitoring is easy to fit and easy to keep an eye on, and the benefits are significant. Think of the possible financial consequences caused by an unforeseen breakdown in production because of a sudden need for a gearbox repair or replacement – plus the loss of customer confidence.
There are other benefits as well as cutting unexpected downtime – maintenance scheduling, for example, is significantly enhanced. Additional features include full reporting for in-depth data analysis; and retention of data for three-years, with historical trend analysis allowing the creation of an ongoing preventative maintenance schedule.
This straightforward system is now integrated into the PLC control system of all new Baker Perkins twin-screw extruders. It can easily be installed as a stand-alone system onto existing machines.