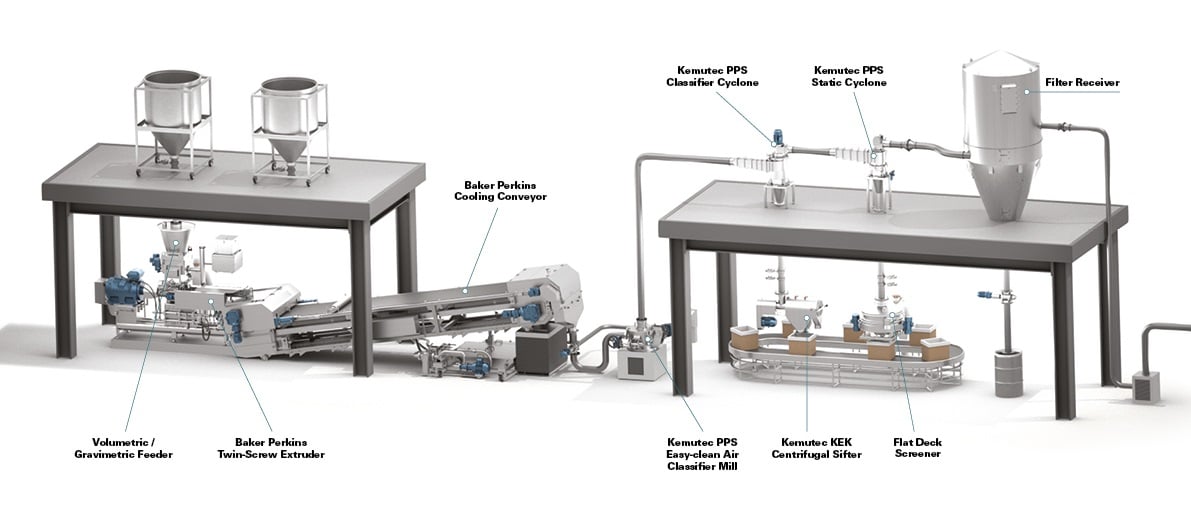
Baker Perkins and Kemutec are global leaders in extrusion and powder processing systems. Working together, we provide fully integrated and automated turnkey systems for powder coatings.
With the addition of Baker Perkins’ new cooling conveyor, manufacturers of powder coatings can now source all their systems from one trusted supplier.
We now manufacture in-house all the equipment for a complete powder coating process line, up and downstream of the extruder: from accurately weighing and feeding the premix, precisely cooling and flaking the extruded material, to milling and sifting all grades of powder coatings, from the coarser grades to the finest.
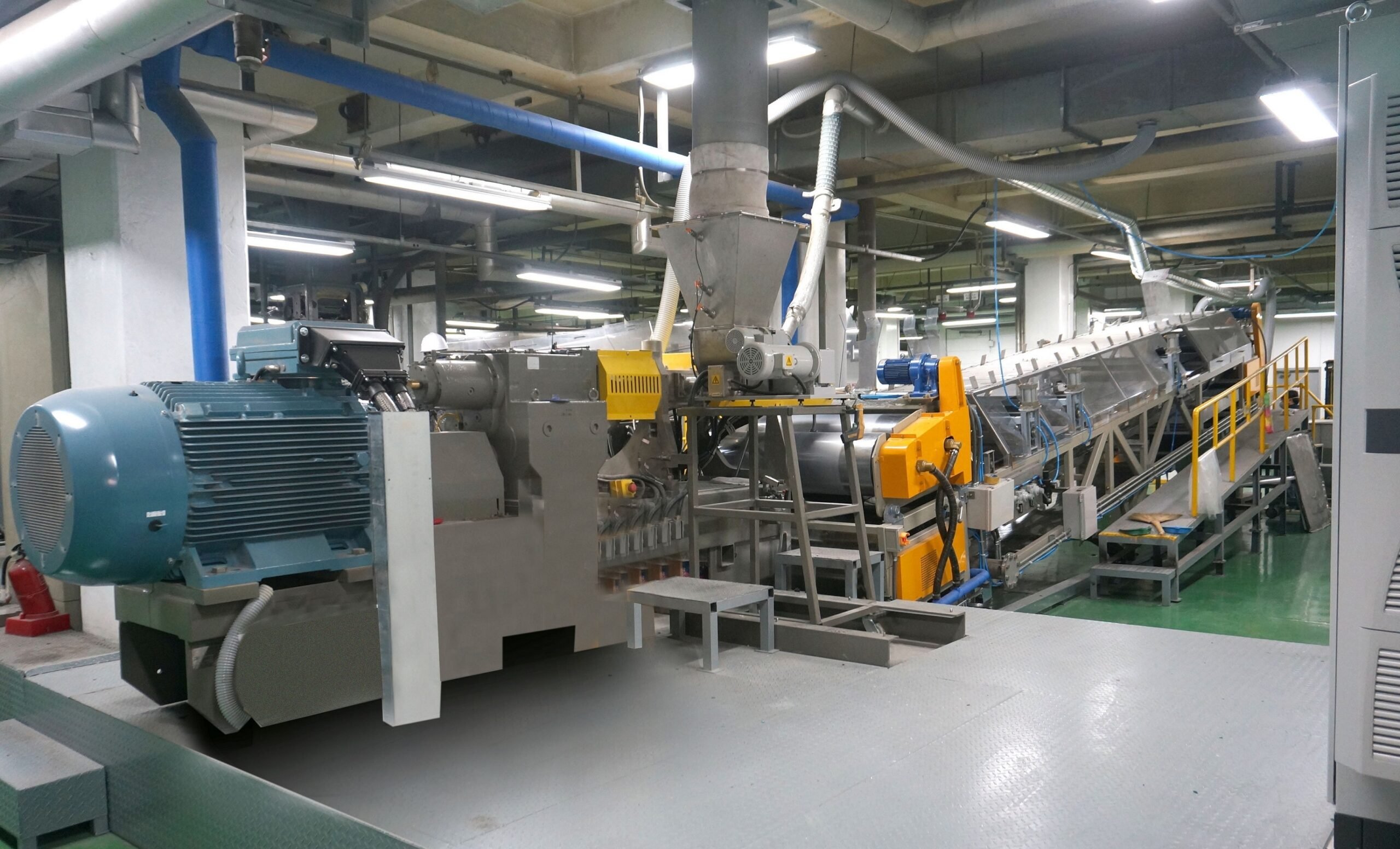
All your processes covered
We can support you from specification and commissioning of easy to operate, clean and maintain equipment, through to development and optimisation in our global Test & Innovation Centres or on-site, backed by comprehensive Aftersales services.
Single source supply offers significant benefits. Working with one company reduces complexities and saves time and money, whilst ensuring a fully integrated system that exactly meets your specification.
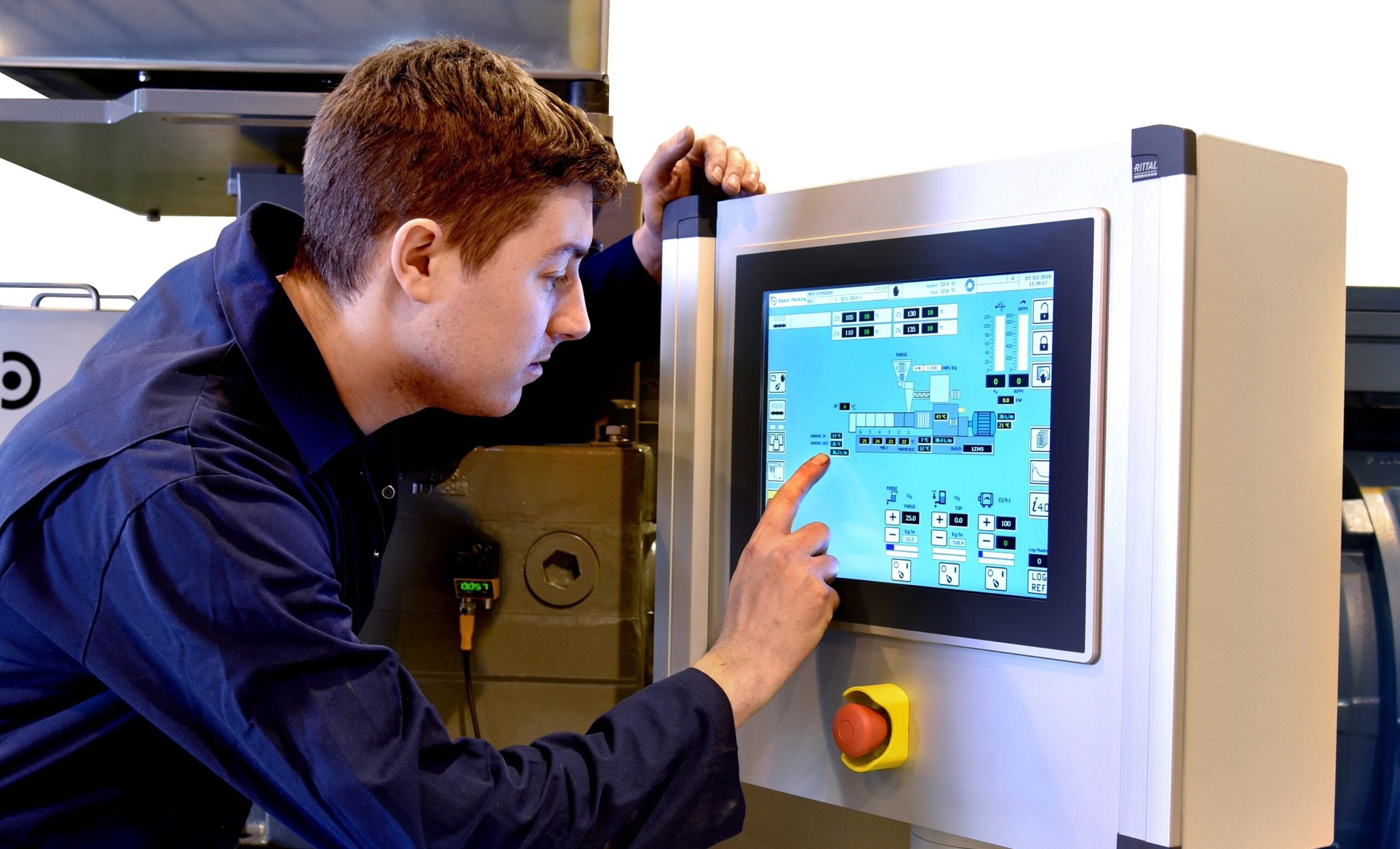
Fully integrated, one control point
Fully integrating a complete powder coating line, with a single control point for the entire system creates substantial opportunities for upgrading performance. It transforms the process from a series of separately controlled functions to one cohesive operation.
Integrated systems have a single touchscreen HMI providing clear, at a glance visualisation of the whole process with real-time feedback on the current status of all major components and parameters. Problems can be resolved quickly, processes can be optimised and set-up, start up and shutdown time can be minimised to reduce labour and waste.
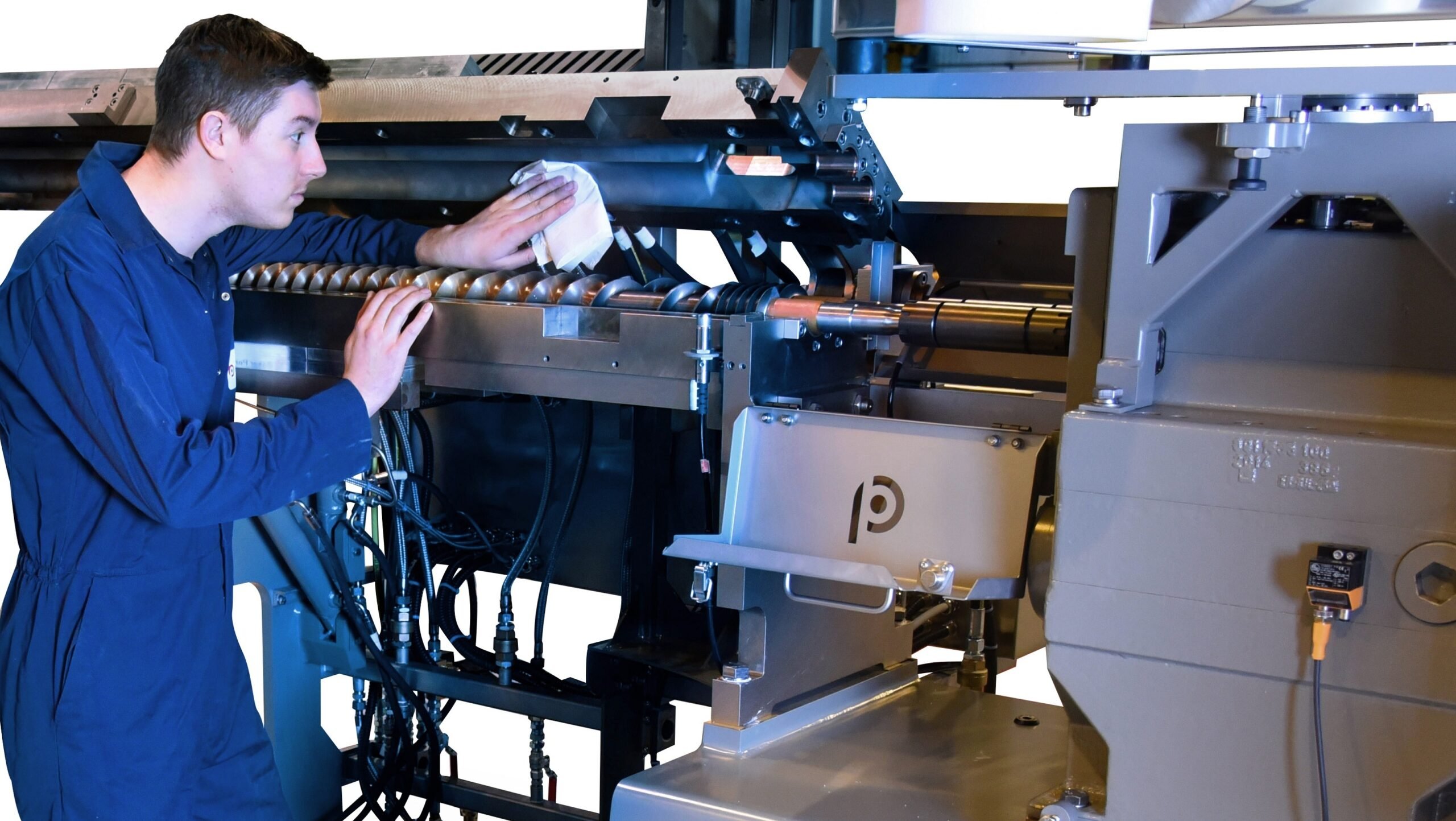
Simple to operate, clean and maintain designs
With our innovative easy-clean designs and patented technologies engineered to enhance efficiency and throughputs, we help manufacturers of powder coatings maintain the highest levels of product consistency.
Whether it is quick resin purges between batches, or deep clean purges between product changes, the automatic system reduces turnaround times, reduces labour requirements and minimises waste. The extruder software takes control to ensure repeatable, quality cleaning regimes. When integrated with upstream and downstream equipment, the system can take control in an emergency event, minimising product waste and equipment downtime; automatically returning to production once the issues have been resolved.
Patented MAX³ technology
The MAX³ feed system successfully addresses the long-standing, industry-wide issue of restricted output and torque surges caused by material building up in the extruder feed port – when particles hit the intake screws and ‘bounce’ back into the infeed area rather than flowing into the machine.
Our patented system introduces a reconfigured feed port and unique screw designs to improve the flow of material into the extruder barrel and the air out of it. A major benefit is that lightweight, low density materials and fines are handled much more efficiently, eliminating the need for side-feeding and its unnecessary floor space, capital and running costs.